410 alarm case study
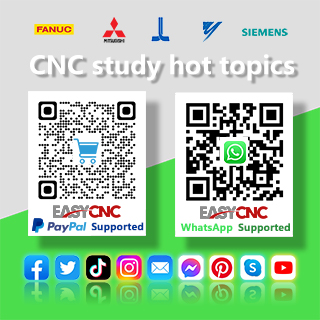
For more details, please check EASYCNC YouTube video here.
410 alarm case study
1. Principle of servo feed system of CNC machine tool
On CNC machine tools, servo feed system is the connection link between CNC device and machine host, which receives feed pulse instructions or feed displacement information generated from the interpolation device or interpolation software, after a certain signal conversion and voltage, power amplification, driven by the servo motor transmission mechanism, and finally converted into linear displacement or rotary displacement of the machine tool table relative to the tool. The block diagram is shown in the figure.
2.Requirements for servo systems in CNC machine tools
CNC machine tool servo feed system as a kind of cutting tool and workpiece movement feed drive and actuator, is an important part of CNC machine tool, it largely determines the performance of CNC machine tool, such as CNC machine tool maximum moving speed, tracking accuracy, positioning accuracy and a series of important indicators depend on the performance of the servo feed system, so the accuracy and stability of the servo system is closely related to the normal work of CNC machine tools, The main performance requirements for the servo drive system of CNC machine tools are as follows:
1. The feed speed range should be large.
2. The displacement accuracy should be high. The displacement accuracy of the servo system refers to the degree of consistency between the displacement amount required by the command pulse to feed the machine tool table and the actual displacement amount of the command pulse converted into the table by the servo system. The smaller the error between the two, the higher the displacement accuracy of the servo system.
3. The following error should be small. That is, the speed response of the servo system is fast.
4. The working stability of the servo system should be good. It is necessary to have strong anti-interference ability to ensure uniform and stable feed speed.
3.Examples of typical failures in servo feed systems
3.1 Example 1
1. Fault phenomenon: equipped with Fanuc 0I-MB system of the American Fado VMC3016L machining center, in the morning students turn on the machine with a handwheel to move the X-axis, the result is servo alarm: 410 SERVO alarm X-axis error is too large and 436 X-axis: SOFTTHERMAL (OVC) alarm is shown in the figure (photo taken during maintenance), shutdown restart mobile X-axis is still the same alarm.
2. Analysis and processing process: check FANUC 0I-MB workshop manual, 410 SERVO alarm: The X-axis error is too large, the possible reason is that the value of the position deviation amount in the X-axis stop exceeds the value set on the parameter (NO.1829). But I took a look at the parameter in 1829 is 1000, and like several other units, it has not been changed, which can rule out the problem of this parameter. 436 X-axis: The explanation of the SOFTTHERMAL (OVC) alarm is that the digital servo detects the software hot state (OVC), I checked the FANUC 0I-MB servo alarm manual, and when the alarm starting with 4 appears, it can be checked by the diagnostic parameter DGN200, as shown in the table.
DGN200
bit7
bit6
bit5
bit4
bit3
bit2
bit1
bit0
Signal Name
OVL
LV
OVC
HCAL
WHALE
DCAL
FBAL
CARE
3. The meaning of the diagnostic parameters is as follows:
OVL: Driver overload alarm; LV: insufficient driver voltage; OVC: driver overcurrent alarm; HCAL: driver current abnormal alarm; HVAL: Driver overvoltage alarm; DCAL: drive DC bus loop alarm; FBAL: drive disconnection alarm; OFAL: Count overflow alarm.
At this time, I switched to the diagnostic screen to find the diagnostic parameter No. 200, and found that bit5=1, and the other digits were all 0, indicating that the drive was overcurrent, indicating that the X-axis servo motor was short-circuited or overloaded, and the resistance between any two phases of the motor plug on the X-axis servo drive was measured with a multimeter was about 2.3 ohms, which was balanced, indicating that the motor was not out of phase, and then measured with a shake meterThe insulation of the X-axis servo motor is also good. There is also a possibility that the internal power amplification module of the X-axis servo drive has a problem, resulting in excessive current, if there is a machine tool of the same model and system can be exchanged for the X-axis servo drive, if not, you can also use a multimeter to roughly measure whether the power amplification module of the servo drive is good or bad. If it is determined that the servo drive is good, it should be that the X-axis servo motor is overloaded, the problem may be in the X-axis mechanical transmission part, this machine tool is the servo motor is connected to the screw through the elastic coupling, the screw has a bearing seat at both ends, one bearing seat is two back-to-back installed angular contact ball bearings (bearing axial and radial forces), and the other end is an ordinary ball bearing (playing a supporting role), so it will be put firstRemove the cover on the right side of the X-axis table, and then remove the X-axis servo motor (see the photo picture taken during maintenance), at this time turn on and move the X-axis, you can see the X-axis servo motor is rotating, indicating that the X-axis servo motor and the servo drive are good, and then I rotate the coupling at one end of the ball screw by hand, under normal circumstances, you can rotate this coupling by hand, and the screw rotates with it, thereby driving the table to move, but I can't rotate the coupling with my hand, as if the screw is stuck, with great forceThe clamp can not rotate, the problem is here, closer and closer to the root cause of the failure, according to past experience, it should be the possibility of the bearings at both ends of the screw to bite to death, and finally check down that the ordinary ball bearing (bearing model: Japan NSK 6304V) rusted to death (see the photo picture taken during maintenance), bought a bearing of the same type on the market to install it back, and the fault was solved.
4. Fault review summary: When the system sends coordinate instructions to the servo feed drive to drive the motor to rotate, but because the ball bearing 6304V rust is stuck, resulting in the screw can not rotate, at this time the motor is seriously overloaded, so there is a 436 X-axis: SOFTTHERMAL (OVC) (overcurrent alarm). At this time, the servo motor did not rotate at all, and the command sent by the system was too different from the amount of position feedback detected by the servo motor code, which exceeded the value set on the parameter (NO.1829), so a 410 SERVO alarm appeared: The X-axis error is too large.
3.2 Example 2
1. Fault phenomenon: Taiwan Liwei TDC510 machining center equipped with Fanuc-0M system X-axis in motion, 414 SERVO alarm: X-axis servo system abnormal, 410 SERVO alarm: X-axis error is too large (as shown in the figure) Photos taken during maintenance, shut down and then turn on, or the same problem, sometimes good, However, the above alarm will appear after processing.
2. Analysis and processing process: from the fault phenomenon can be judged that the X-axis servo feed system has a problem, is because of the 414 X-axis servo system abnormal alarm, only then there is a 410 X-axis error too large alarm, according to the above introduction of the servo feed system principle, you can know that once the servo system abnormality, resulting in the actual movement and the system pulse amount is very different, only then there is a 410 axis error too large alarm, that is, as long as the 414 alarm is solved, The 410 alarm is gone. I checked the FANUC 0M servo alarm manual, and when the alarm starting with 4 appears, it can be checked by the diagnostic parameter DGN720 (Note: FANUC 0I series CNC system servo diagnosis number is 200, FANUC 0 series CNC system servo diagnosis number is 720 start), as shown in the table.
DGN720
bit7
bit6
bit5
bit4
bit3
bit2
bit1
bit0
Signal Name
OVL
LV
OVC
HCAL
WHALE
DCA
FBAL
CARE
At this time, I switched to the diagnostic screen to find the 720 diagnostic parameters, and found that bit5=1 (OVC: driver overcurrent alarm), the other digits are all 0, indicating that the driver is overcurrent, the X-axis servo motor is short-circuited or overloaded, and the resistance between any two phases of the motor plug on the X-axis servo drive is about 3.4 ohms with a multimeter, which is balanced, indicating that the motor is not out of phase, and then measured with a shake meterX-axis servo motor any relative shell resistance value is very small, only about 1M ohms, indicating that the servo motor insulation is seriously deteriorated, the following to find the reason for the insulation deterioration, according to past experience, may be the motor connection line aging, there is a broken place, check the motor connection line, are normal, no broken place. There are also problems at the quick plug connector of the motor, and as a result, when I unplug the motor quick plug connector (as shown in the picture), I pour out some cutting fluid from the plug, which is the reason for the serious deterioration of the insulation of the motor, for the insurance period, I useThe shake meter directly measures the insulation of the phase wire on the plug of the motor root to the motor shell, and the measurement is normal, indicating that the servo motor has not burned, and has encountered similar failures before, but also because of water entering the plug, and then entering the inside of the motor, causing water, burning the servo motor, and then the servo motor is rewound to eliminate the fault. Finally, the water inside the quick plug connector of the servo motor was blown off, and a small hole was drilled under the quick plug connector, if there was standing water, it could leak down, and no such failure was found in the future.
3. Fault review summary: more fortunate that the fault did not burn the servo motor, if the worker opens the machine a few more times, moves the X axis a few more times, then it is possible to burn out the servo motor, short-term servo motor overload does not matter, afraid of long-term overload, like at the beginning to hear the motor vibration or hum or smell burnt paste, the following do not power on, to check the cause of the failure, if the power on, will lead to serious consequences, or burn the servo motor or burn the servo drive.
4 Conclusion
In actual production, the failure of CNC machine tools is mostly the fault of CNC servo feed system, involving servo drives, servo motors, transmission mechanisms (ball screw nut pairs, couplings, bearings, etc.), feedback devices, etc., the causes and forms of failure are diverse, but because the self-diagnosis technology of full-function CNC machine tools is becoming more and more comprehensive, the self-diagnosis ability is getting stronger and stronger, and the original simple diagnosis is developing in the direction of multi-function and intelligence. Once a fault occurs, with the help of the system's self-diagnosis function, the cause can often be quickly and accurately identified and the fault site can be determined. Next, I will analyze the typical fault examples of the servo feed system I have repaired in a serial way for peers to communicate with each other.